Instant Quotation for your Milled Parts
On this page you will find our help for creating an instant quotation for your milled parts. Errors can occur, which you can easily rectify with the help of a few tips. In this way, we ensure our quality so that you do not order faulty parts. Find out more in our design tips.
If you still have questions about meviy, please contact our meviy support.
Common errors when creating a quote with meviy
The uploaded 3D-CAD file could not be read by meviy
If you encounter following error codes
1. the file format could not be read
2. PMI could not be calculated
this means that you are using 3D CAD formats and extensions that are not supported by meviy. To solve this problem, we recommend that you check and adjust the list of formats supported by meviy.
- Autodesk Inventor 2023 + previous versions (.ipt)
- CATIA V5-6R2022 + previous versions (.CATpart)
- Creo - Pro/E 19.0-Creo 9.0 (.prt/.neu/.xpr)
- NX - Unigraphics (.prt)
- SolidEdge V19-20/ST10 + previous versions (.par/.pwd)
- SOLIDWORKS 2023 + previous versions (.sldprt)
- I-deas (.arc/.unv)
- iCAD SX V8L3 + previous versions (.icd)
- STEP AP203, AP214 (.step/.stp)
- Parasolid (.x_t/.x_b/.xmt/.xmt_txt)
- ACIS (.sat/.sab)
- JT (.jt)
- PRC (.prc
Unsupported Shapes
This error is caused by uploading a form that is not available for an instant quote with meviy. To solve this problem, please check the available forms that we can offer with meviy.
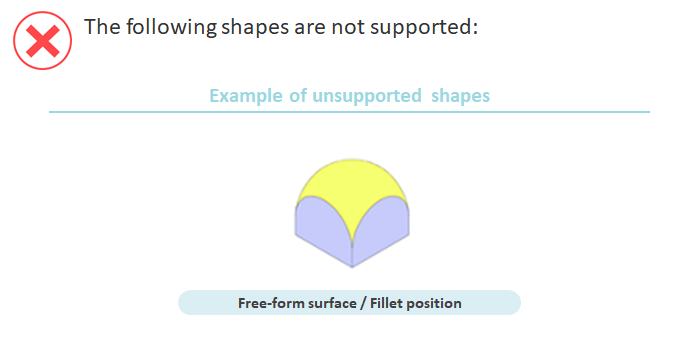
Size exceeds instant offer range
This error is caused by the size of the uploaded part. If the uploaded part is outside the size for the instant quote area, no quote can be created. In this case, the dimensions of the part must be adjusted. Please check our available sizes.
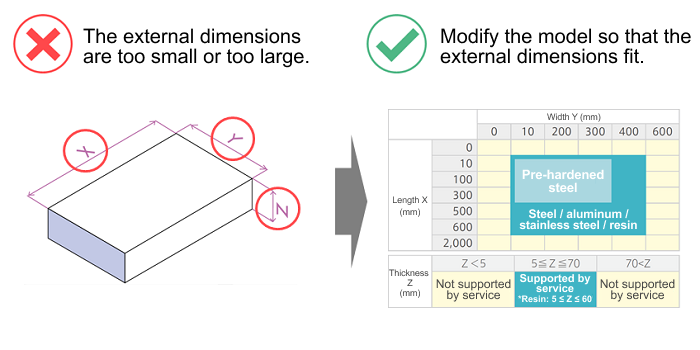
Unsupported holes
This error occurs when a part is uploaded whose hole types cannot be recognized by our meviy system. In this case, the hole is not supported and must be changed to one of the supported hole types. Please check our available hole types.
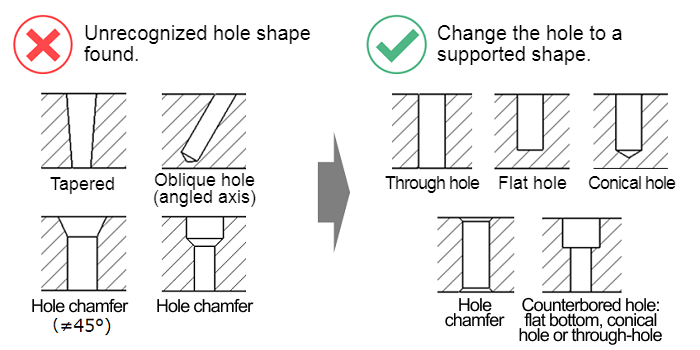
Unsupported pocket depth
Such an error occurs when the corner radius within the so-called pocket cannot be manufactured with the given tools. To solve this problem, it is advisable to adjust the corner radius accordingly. One way of doing this would be to increase the corner radius so that the milling cutter can manufacture the corner radius.
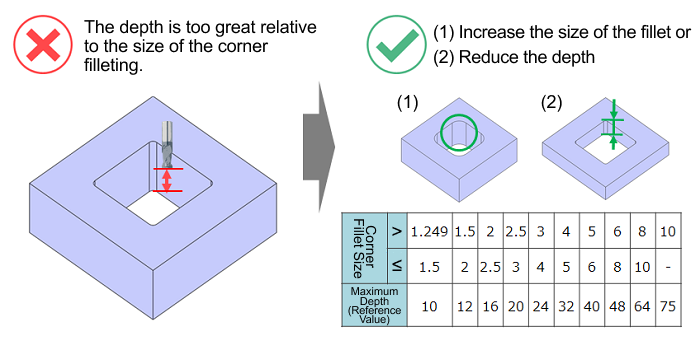
Pocket width/depth not permitted
This error occurs if the specified machining depth is deeper than the width of the pocket allows. The tool diameter is determined by the minimum pocket width. A smaller pocket width means that a narrower end mill must be selected, preventing deeper machining. To solve this problem, it is advisable to increase the pocket width or reduce the pocket depth. By increasing the pocket width or reducing the pocket depth, you can ensure that machining can be carried out properly.
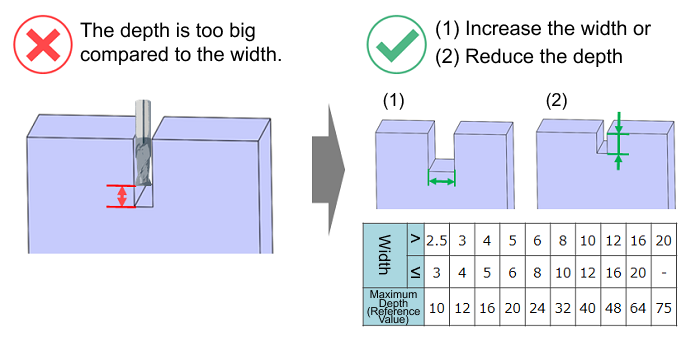
Depth of the hole cannot be manufactured
This error occurs when the hole is deeper than intended, which can lead to a collision between the spindle and the workpiece. To eliminate this problem, it is advisable to adjust the depth, diameter or position of the hole to avoid a collision and ensure a smooth machining process.
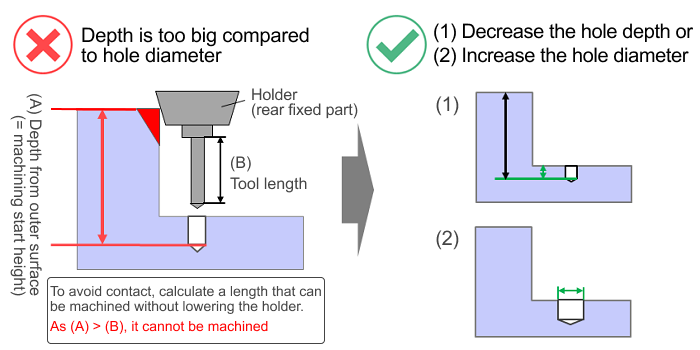
Corner brackets cannot be manufactured by machine
This error occurs if an inner corner angle does not have a radius and therefore a radius remains in the corners. To correct this problem, the suggested radius can be used to round the corner. Alternatively, it may be necessary to adapt the design in order to shape the corner so that it meets the requirements and does not have any unwanted radii.
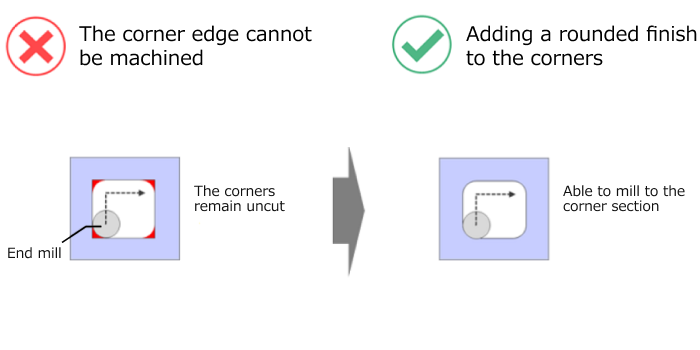
Design Tips for CNC-Milling Parts: Pockets and Radii
The design of the pockets and the corresponding corner radii is of paramount importance. These aspects not only contribute to the overall aesthetic effect, but also play a crucial role in ensuring optimal functionality and manufacturability of individual milled parts. In this section, we will look at basic design knowledge and guide you through the art of creating pockets in milled parts that seamlessly combine form and function while taking into account the intricacies of corner radii. To help you create an instant quote for your specific milled part, we'll explore three different types of pockets: closed pockets, open pockets and stepped pockets.
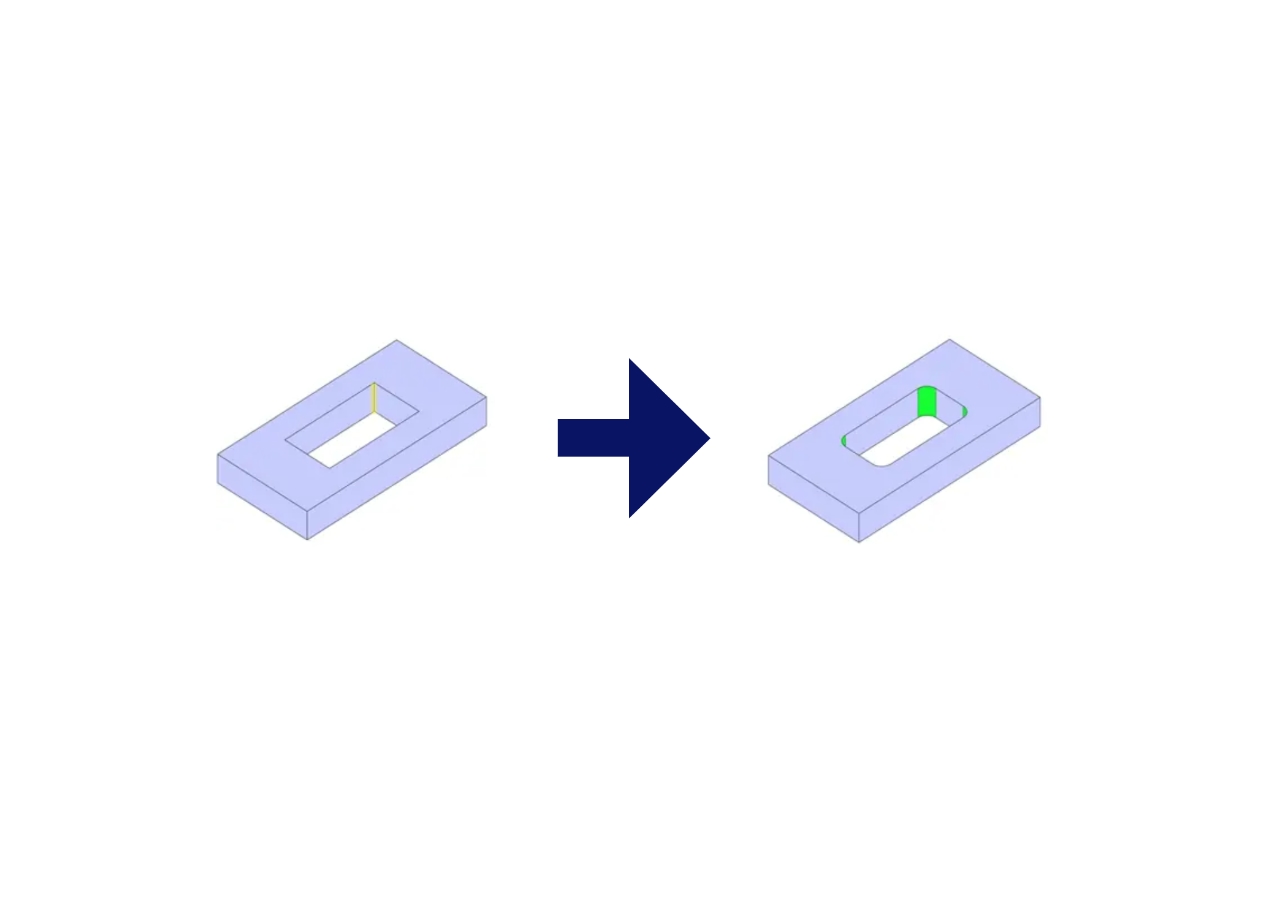
Closed pockets
In a closed pocket, where all four sides are closed, the movement of the end mill follows a pattern as shown in the illustration. This type of movement means that angles smaller than the end mill diameter cannot be machined. For this reason, it is essential to provide an inside radius at all four corners.
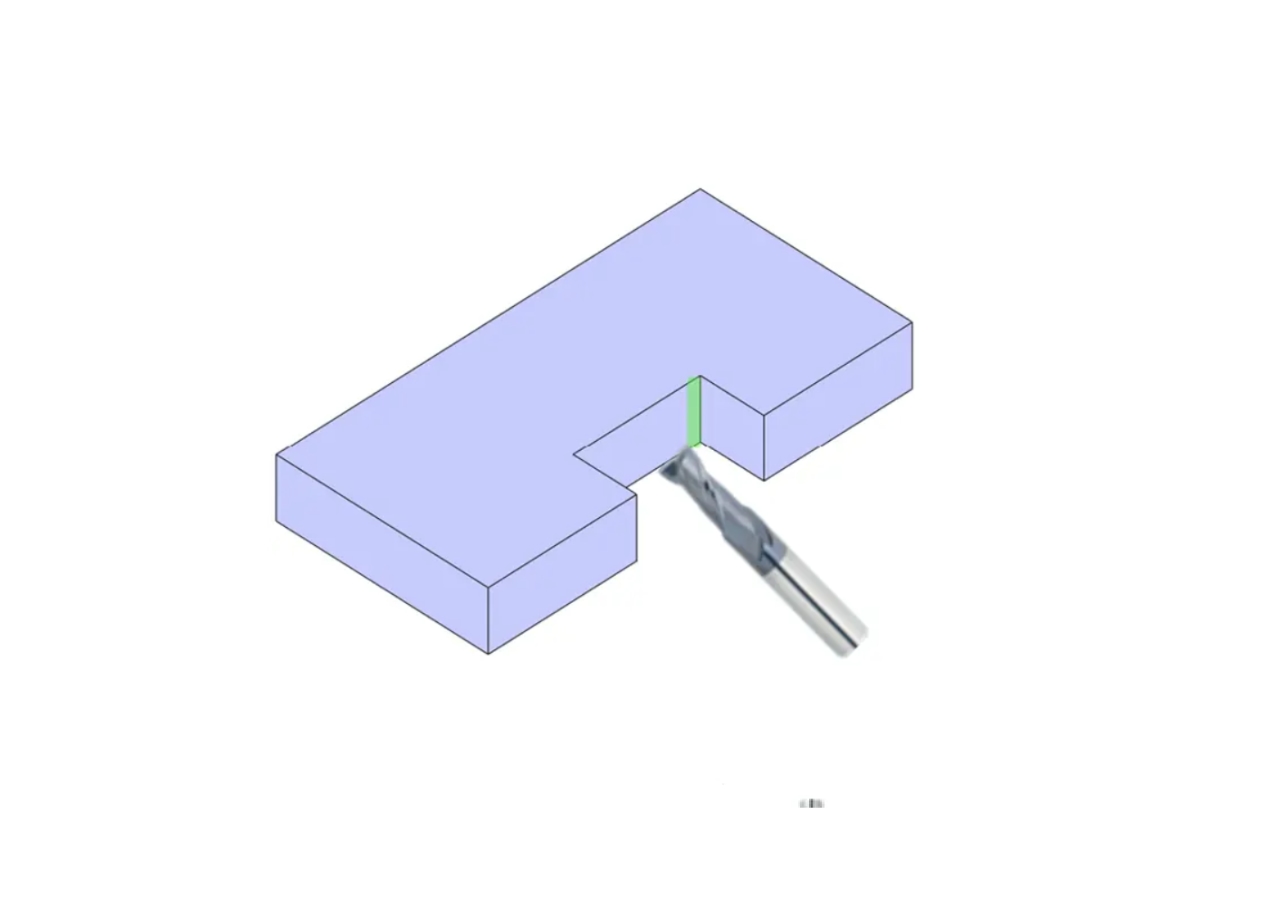
Open pockets
In an open pocket, where the four surrounding sides are not closed, it is possible to machine pocket shapes without an inner radius, as these can be machined horizontally. However, this requires careful planning of the entry direction of the cutting tool.
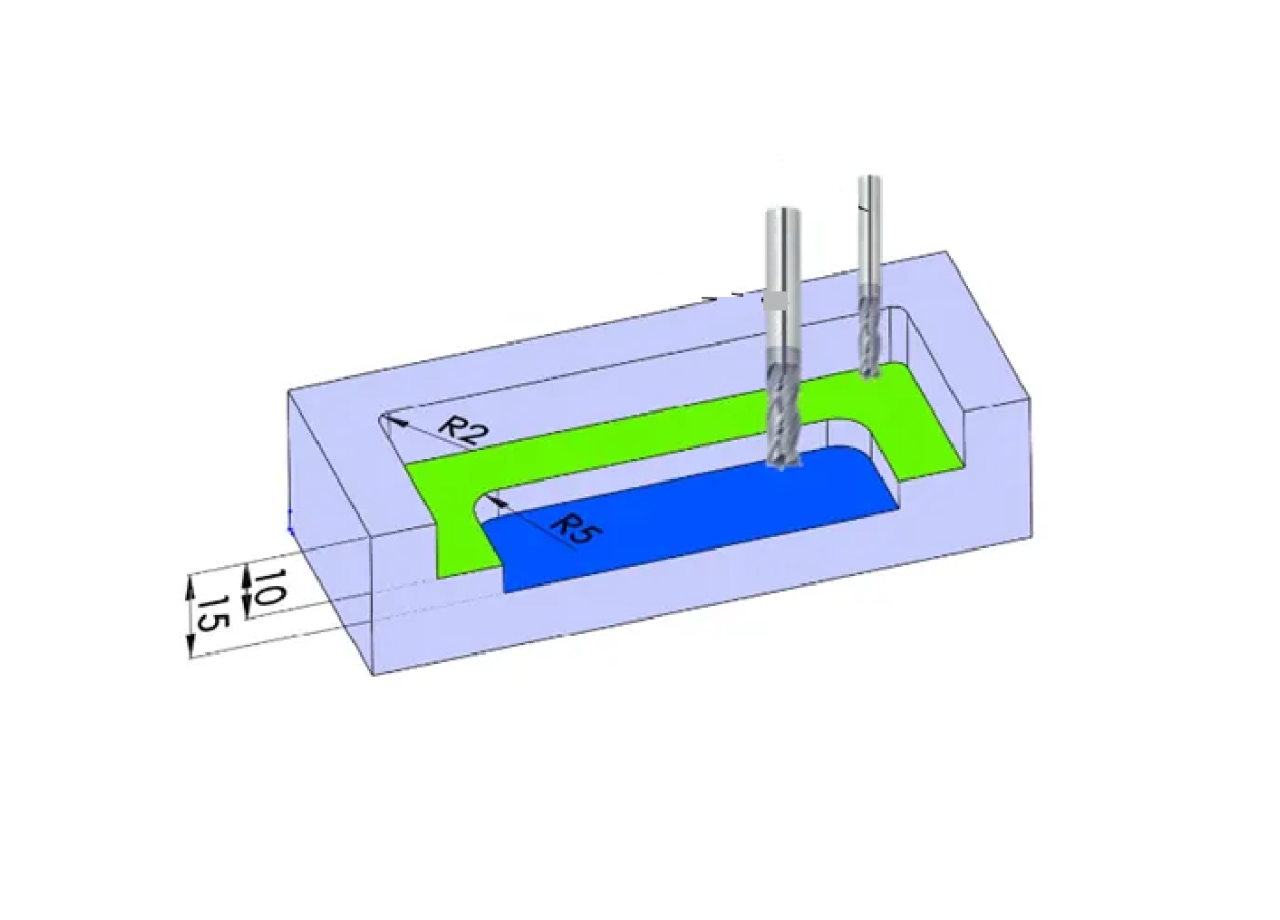
Stepped pocket
With a stepped pocket, as shown below, the flatter pocket is specified with a corner radius of R2. This enables machining with an end mill designed for a radius of R2. The deeper pocket, on the other hand, is specified with a corner radius of R5 and requires correspondingly adapted machining tools. As the depth increases, an end mill with a larger diameter is required, which ensures careful machining.
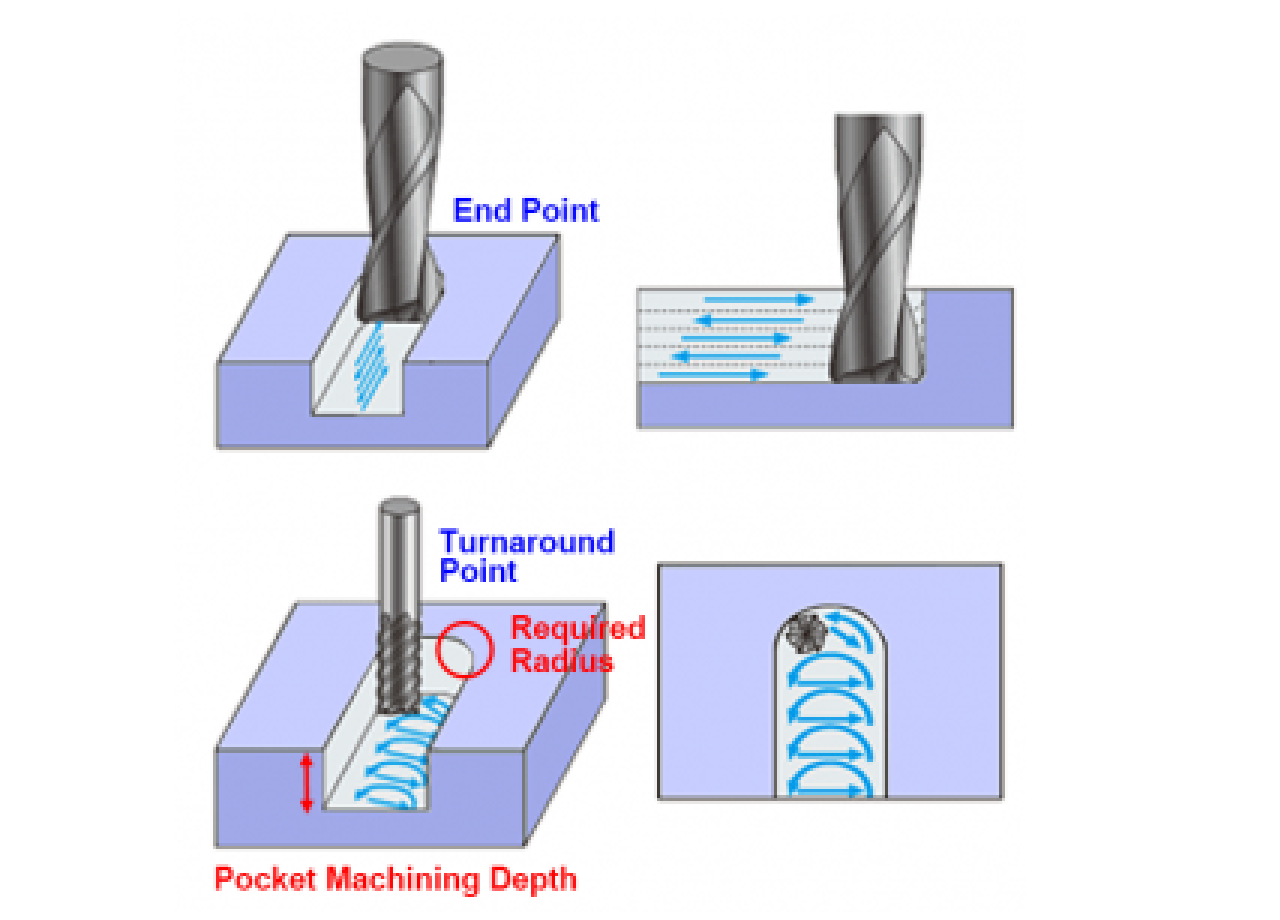
Radius at the turning point of the end mill
A radius corresponding to the end mill is always required at the end and turning points of the end mill. The following figure illustrates the behavior of the end mill at these points. The required radius value varies depending on the depth of the pocket in order to enable machining with the optimum diameter of the end mill.